From Downtime to Uptime: How Centerlining Transformed Our Operations.
Transform your Operations with Centerlining
Stop Struggling with Downtime, Inefficiency, and Process Standardization
38%
INCREASE in Overall Equipment Effectiveness
Standardizing machine settings and optimizing processes ultimately minimizes downtime, improves product quality, and fosters a culture of continuous improvement.
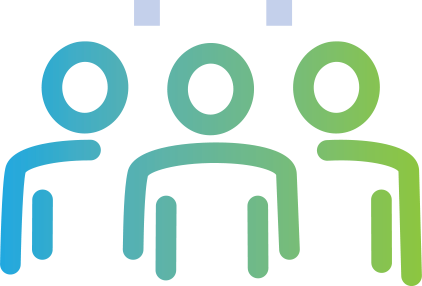
Reduced Downtime and Changeover Times
More consistent and reliable production schedules increased production capacity and the ability to reliably meet customer demands.
18%
Improved Employee Experience
With clear guidelines and standardizations in place, employee stress and frustration were reduced. This contributed to less turnover, lessening hiring costs and disruptions.
The Solutions
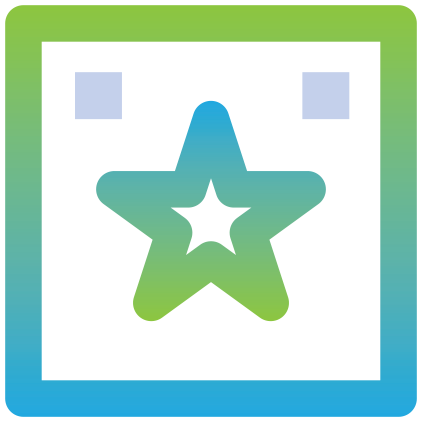
Ensure consistency and standardization across all manufacturing sites.
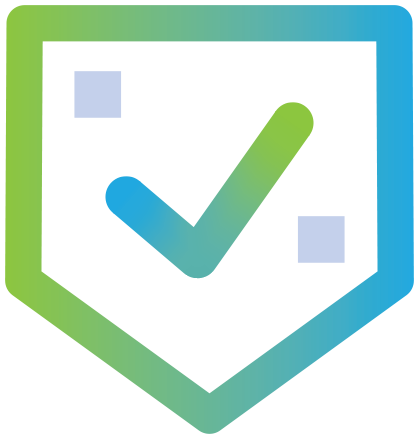
Provide staff the means to implement centerlining effectively on an on-going basis.
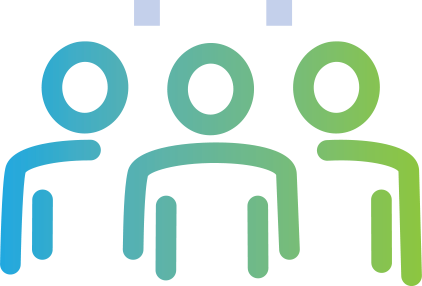
Working side-by-side with client staff, GMP Pros collects data to identify areas of improvement and develop master setup sheets.
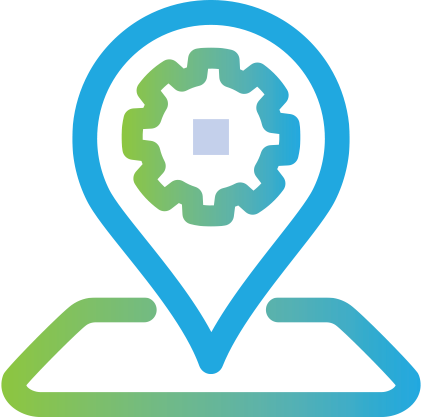
A step-by-step playbook for setting up production lines quickly and effectively, every time.
Ready to Boost Your Production Efficiency with Centerlining?
Embrace Continuous Improvement: Let’s identify opportunities for improvement across your organization. By implementing solutions like centerlining, GMP Pros can help you can achieve operational excellence and drive long-term growth.
Prepare for Long-Term Success: Implementation process improvements are not a one-time endeavor. By partnering with GMP Pros, your business can maintain the commitment to continuous improvement and remain accountable for maintaining high standards.